In a previous post, we looked at why propellers have different numbers of blades, but there are also various designs which affect how propellers function, and improve aircraft efficiency and performance. Propeller blades are basically a set of aerofoils arranged radially around a shaft. Just like wing aerofoils produce lift, propeller aerofoils also generate a form of ‘lift’ excepting that they don’t lift the aeroplane ‘up’, instead they spin on an axis, and ‘pull’ it forwards.
Let’s have a look at the different types of propellers…
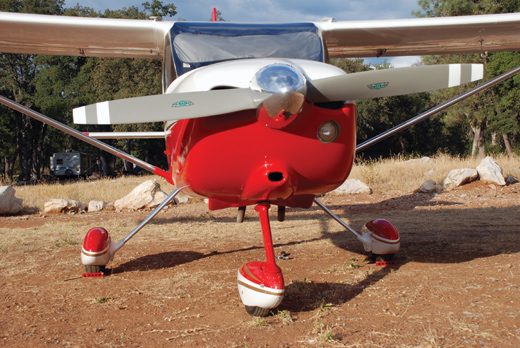
Fixed Pitch
The most basic of all the propellers, this one requires no pilot intervention, because as the name suggests, the blades are fixed at a set angle of attack, and that is the way they will stay. The angles cannot be adjusted in flight, which means that the designers and builders have to pick the average pitch (the angle between the chord line of the blade and the rotation plane) that will perform best over varying phases of flight.
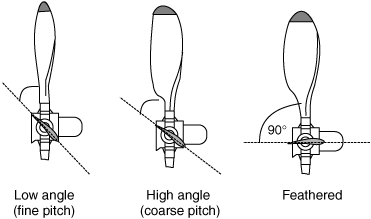
To understand this, a low, or small angle (the prop blade is turned only a little or ‘fine‘), will ‘grab’ a smaller amount of air, which mean that it will be able to rotate faster. Therefore, a fine pitch is ideal for lower speed phases, like the take-off, where we start slow and want to reach acceleration quickly. On the other side of the spectrum, if we turn the blade more, we will have a greater or ‘coarse’ pitch angle. This moves a big chunk of air, but because of the resistance the blade surface presents, it will rotate at a slower rate initially, but in cruise flight, it will get the aeroplane moving a greater distance through the air for every rotation of the propeller. A fixed pitch propeller will never offer you the best take-off, nor be the most efficient in cruise, because the pitch cannot be changed in flight. Aircraft that use these are likely to be pretty slow, single engines.
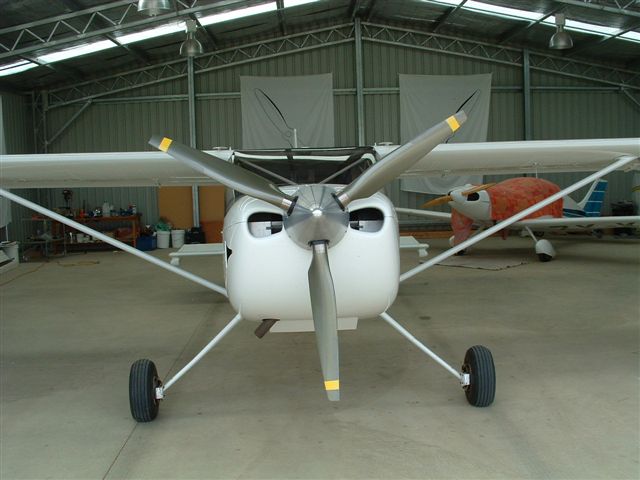
Variable Pitch
The obvious advancement on the fixed pitch, was to create a propeller that could be adjusted in flight to ensure the best performance, based on the phase of flight. These are not a new invention. The French aircraft firm Levasseur displayed a variable-pitch propeller at the 1921 Paris Airshow, which, it claimed, had been tested by the French government in a ten-hour run and could change pitch at any engine RPM (Source: Wikipedia). Adjustment of the pitch is carried out by the pilot, using the ‘pitch’ lever, usually in accordance with a specific RPM indicated value. Knowing which way to pull or push the lever is imperative for correct operation and maximised efficiency.
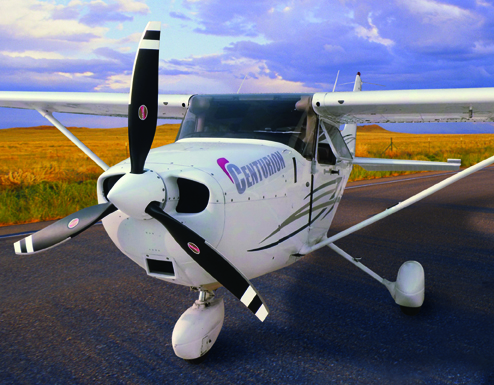
Constant Speed Propeller
The variable pitch was a wonderful idea, excepting for the increased pilot workload – so, a new star was born in the form of the constant speed propeller. This takes the concept of a variable pitch, and automates it, in order to change the pitch of he blades, so as to maintain a constant RPM, regardless of the conditions. This is achieved through the work of a constant speed unit – a device which mechanically alters the pitch angle to maintain the RPM, using centrifugal force to balance out over or under speed. The beauty of this type of propeller, is that if the thrust is reduced, RPM is reduced accordingly, and the opposite if thrust is increased. Not only does this propeller improve efficiency, it also reduces the strain on the engine and other working parts.