If you have ever felt a little confused as to how carb heat works, and when exactly to use it, you are not alone. Many more modern aircraft have fuel injected systems, so if you ever step into an aircraft of an older vintage, that has a carburettor system, it is important to understand what carb heat does and when to use it.
In piston engine aircraft with internal combustion engines, the carburettor is a device responsible for the maintenance of the proper air to fuel ratio for combustion. The carburettor works on Bernoulli’s principle, in that the faster air moves, the lower its static pressure, and the higher the dynamic pressure is. The throttle does not directly control the flow of liquid fuel. Instead, it actuates carburettor mechanisms which meter the flow of air being carried into the engine. The speed of this flow, and therefore its (static) pressure, determines the amount of fuel drawn into the airstream (1).
Clearly, if the carburettor stops working, we have a problem which affects the proper running of the engine, and could ultimately end in an engine failure.
What would cause the carburettor to stop functioning?
The most common cause is icing. As air enters the carburettor venturi, pressure is reduced which leads to cooling. At the same time, the fuel undergoes a process of vapourisation, and in the transformation, latent heat is absorbed resulting in cooling all around it. The result being, the venturi throat of the carburettor can be cooled to a temperature below freezing. Water vapour will freeze if it comes into contact with the surface of the throttle valve, leading to ice build up.
However, there are additional atmospheric considerations which are often forgotten, or ill-considered by pilots. The first is the relative humidity of the air – the higher the relative humidity, the increased risk of icing, due to the greater presence of water vapour. Relative humidity 80% and above provides the greatest risk. Apart from confirming the relative humidity through weather reports and forecasts, the visual evidence of greater relative humidity, is the presence of clouds.
The next confusing bit is the outside temperature. The assumption is that if the outside air temperature (OAT) is above zero degrees, we will not have icing.
We must be reminded here, that it is not the air temperature which causes cooling in the carburettor, but rather the pressure drop and the heat which is absorbed during the vapourisation of fuel. This means that warm air, which is already less dense, and has a lower pressure, can still lead to carb icing IF the relative humidity is high.
In fact, the riskiest temperature range for carb icing is in the region of -7°C and +21°C (but can occur anywhere between -15°C and +30°C) with a relative humidity above 80%.
What are the symptoms of carb icing?
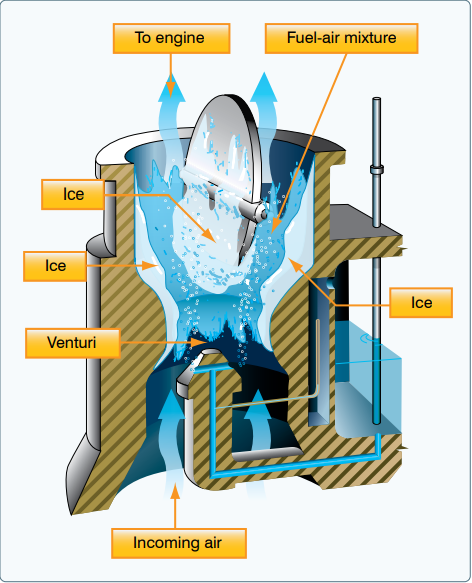
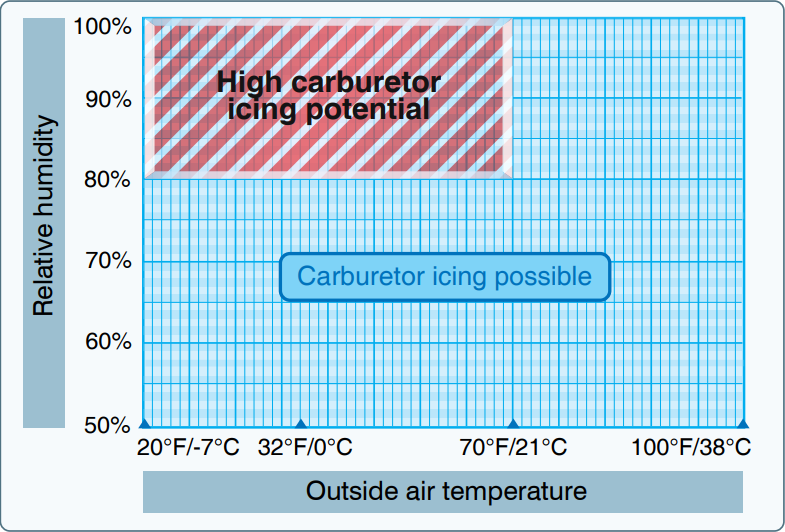
- Gradual loss of power – No change in RPM if a CSU is fitted, but manifold pressure will show a reduction.
- Rough running engine – Ice blocking the intakes will result in a richer mixture, which could result in a complete loss power.
- Lower Exhaust Gas Temperature (EGT).
- Jammed throttle.
Carb heat can both prevent the problem, and eliminate it, provided the pilot uses it correctly. The carb heat system draws hot air from the heat exchanger or from the exhaust manifold (systems vary between aircraft), which is then directed to the venturi. It is then heated up to prevent the formation of ice, or to melt any ice.
When to use carb heat?
- When icing conditions are present.
- High relative humidity.
- Prolonged descent, or when approaching to land at low RPM.
- When significantly reducing power (for example a simulated forced landing)
There is, however, a major disadvantage to using carb heat, because it feeds warm air to the engine, the mass of air is less (warm air is less dense), and therefore the power that the engine is able to produce will also be reduced. This can pose a particular problem if low to ground, or in the situation of a go-around.
If carb heat is applied in the cruise, this will result in decreased air pressure, which may necessitate a leaning of the mixture, as there would be too much fuel relative to the mass of air coming into the engine.
The opposite would occur in a continuous descent, where, as we descend, the air becomes denser naturally. So even if we have carb heat on, the air mass entering may become too much for the amount of fuel being provided, In this case, it would be advisable to monitor the EGT or cylinder head temperatures – if the temperatures become high, it will be necessary to increase the mixture until the temperatures come back within the normal range, or as stated in the aircraft POH.
Lastly, if you do experience icing and apply carb heat, the rough running will initially sound worse, but don’t be tempted to put it off! Leave it on until the rough running ceases, and once out of icing conditions.
Images: Wikipedia, Craig Steffen
Awesome explenation thank you.
So will it help if i apply carb heat if CHTs trmps rn high?
Jabiru has carb heat but no mixture cotrol.
Can i fly on a hit day in cruise with carb heat on for long duration?
Yes, if it’s necessary i.e. you’re getting continuous carb icing. If this is the case, you will need to adjust the mixture to get the best engine performance, usually it needs to be leaner as the (hot) air is less dense. If you don’t have an EGT gauge to work with, then watch for best RPM, then enrich the mixture just a little.
thank you for the information
Great tips even for a pilot who has flown a number of years. Good reminder on all the factors.