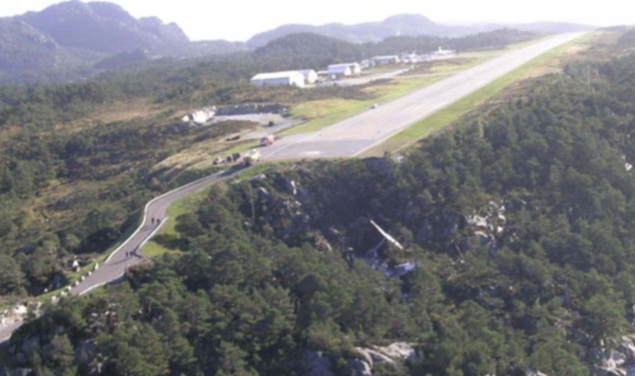
Photo: (AIBN)
Wet runways can be hazardous, especially on landing, as the reaction of the aircraft is not always predictable. The surface of the runway, the depth of the moisture, the type of tyres and pressure, all affect how the aircraft will handle after touch down. Hydroplaning is a very real threat, whereby braking becomes ineffective as the tyres of the aircraft are lifted and ‘carried’ by the moisture on the runway. When water is visible on the runway, precautions can be taken, but did you know that even the slightest amount of barely-there moisture on a runway surface can be far more dangerous than it looks?
Reverted rubber hydroplaning occurs through a situation of heavy braking where wheels lock up, and the tyre contact point with the runway becomes so hot that the rubber begins to melt. Even the smallest amount of moisture trapped beneath the tyres will quickly turn to steam. The tyres are then lifted by this steam, causing the aircraft to hydroplane. Braking becomes ineffective, and controlling the aircraft a tangible challenge.
To highlight the impact of reverted rubber hydroplaning, we can look at one of the best known aircraft crashes, where investigators found this form of hydroplaning, along with some other factors to have been the leading cause. Here we refer to the crash on 10 October 2006 at Stord Airport, Sørstokken, Norway, when Atlantic Airways Flight 670 (a British Aerospace 146-200A) experienced a runway overrun on landing, and went down a steep slope, causing considerable damage, eventually bursting into flames leaving only twelve survivors.
According to the report, the accident was initiated after landing when the lift spoilers (which are used to counter the natural inclination of the wings to produce lift, increase the weight force on the wheels required in order to produce friction and bring the aircraft to a stop) were not deployed. This, in itself, was not sufficient to cause the aircraft to overrun, as such a failure is anticipated when landing distance required (LDR) is calculated, and the aircraft would have had sufficient landing distance available. However, it was deduced that the pilots perceived this to be a wheel brake failure and proceeded to deploy the emergency brakes. While the aircraft was equipped with an anti-skid system (which generally prevents the wheels from locking up), once the emergency brake is activated, the anti-skid is no longer operational. The most significant factor of this accident to our topic is that the runway was damp. Once the emergency brakes were activated, the wheels locked up, causing the tyres to heat up sufficiently for the moisture on the runway to evaporate, and form steam which lead to reverted rubber hydroplaning.
The investigation also revealed that the airport held several factors which contributed towards the accident. Notably, the runway surface did not have grooves extending across, which would have assisted in aiding braking, and channeling any moisture off the surface. Secondly, the safety area at the end of the runway was only 130m, followed by a very steep wooded slope, which was inaccessible to emergency services. Pilot training on braking systems was since improved, as well as the airport facilities.
So, in our smaller aircraft, which are most commonly not equipped with anti-skid systems, how can we prevent hydroplaning, and more especially reverted rubber hydroplaning? Firstly, you always want to check your aircraft’s performance graphs to make sure that you have enough LDA in comparison to LDR for your aircraft weight, especially in wet conditions. If the runway is very wet, you will want to be assured that your tyres are correctly inflated and definitely not on the soft side. Secondly, try to land firmly, so that your tyres make good contact with the surface (weight on the wheels produces friction), but NOT fast, as this could pronounce the effect of hydroplaning. Avoid using excessive braking action, and instead use your aerodynamic tools as much as possible to slow the aircraft down.
Even when the runway is just damp, only apply a little braking to prevent the wheels from locking up, and instead use flaps (or any other aerodynamic device at your disposal) to reduce aircraft speed. Try to get as much weight on the landing wheels as possible, and if you have the option of more than one suitable runway, choose the option that offers the most friction, and uphill slope.